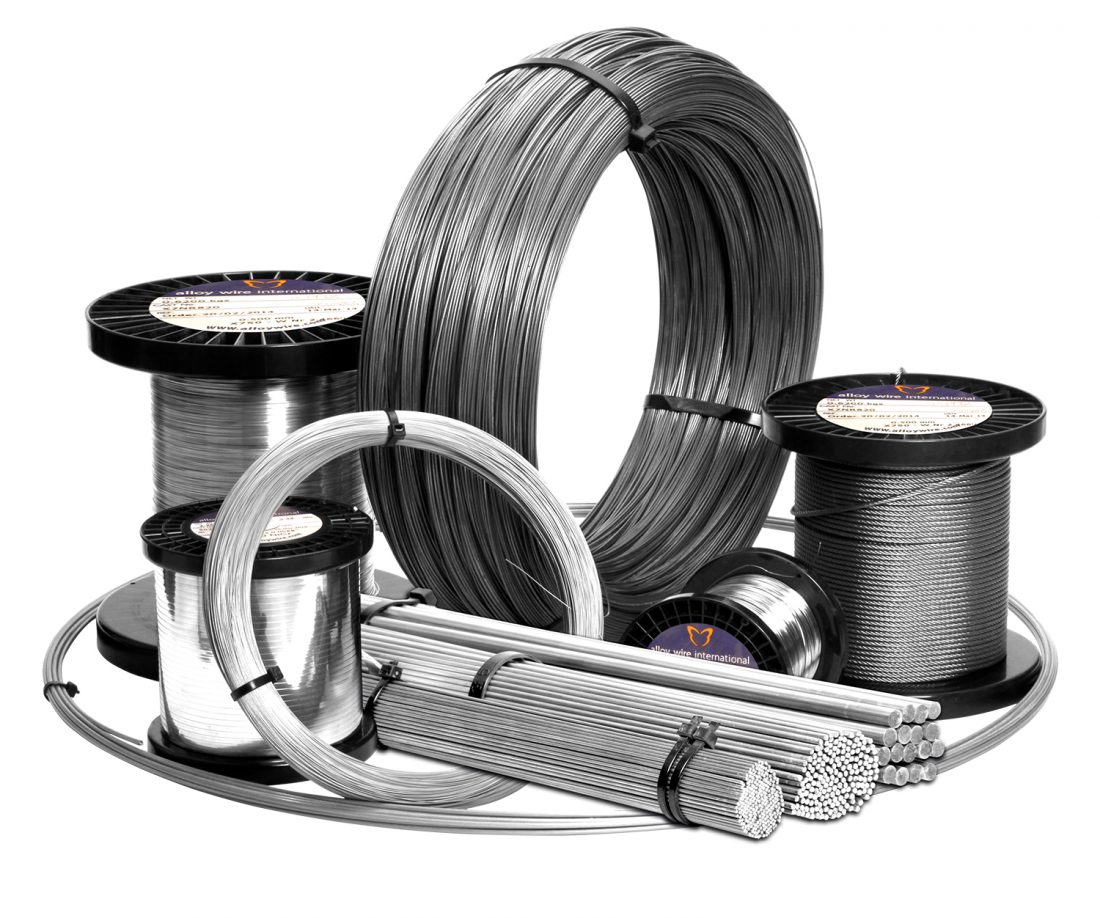
Inconel® X750
Inconel® X750 is a Nickel-Chromium alloy made precipitation hardenable by additions of Aluminium and Titanium, having creep-rupture strength at high temperatures to about 700°C (1290°F). It is widely used for high temperature conditions but is not as strong as Nimonic 90, but Inconel® X750 also holds exceptional properties all the way down to cryogenic temperatures.