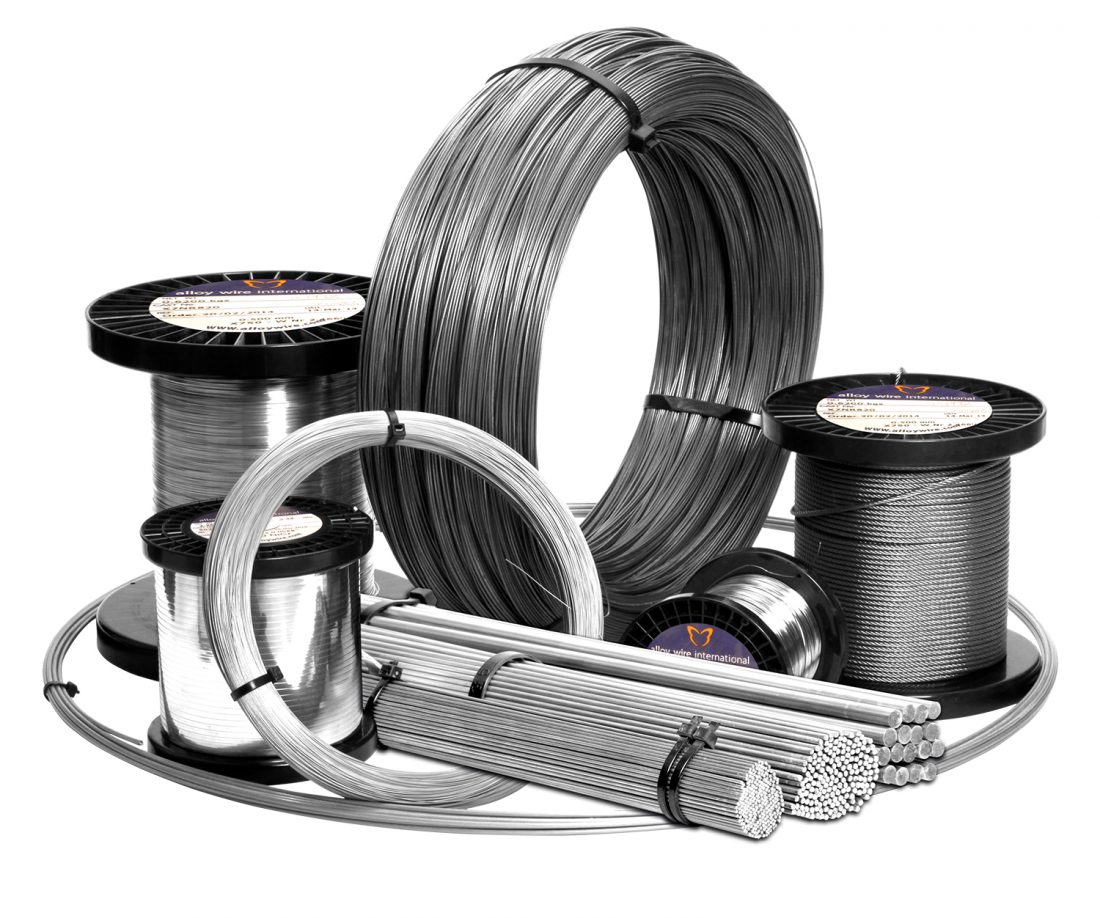
Rene 41
Rene 41 is an age hardenable nickel base alloy that has very high strength at elevated temperatures, particularly within the range of 650 - 980 °C (1200 - 1800 °F). Required mechanical properties can be tailored by selection of various combinations of cold work and/or heat treatments. Rene 41 also has good oxidation resistance.