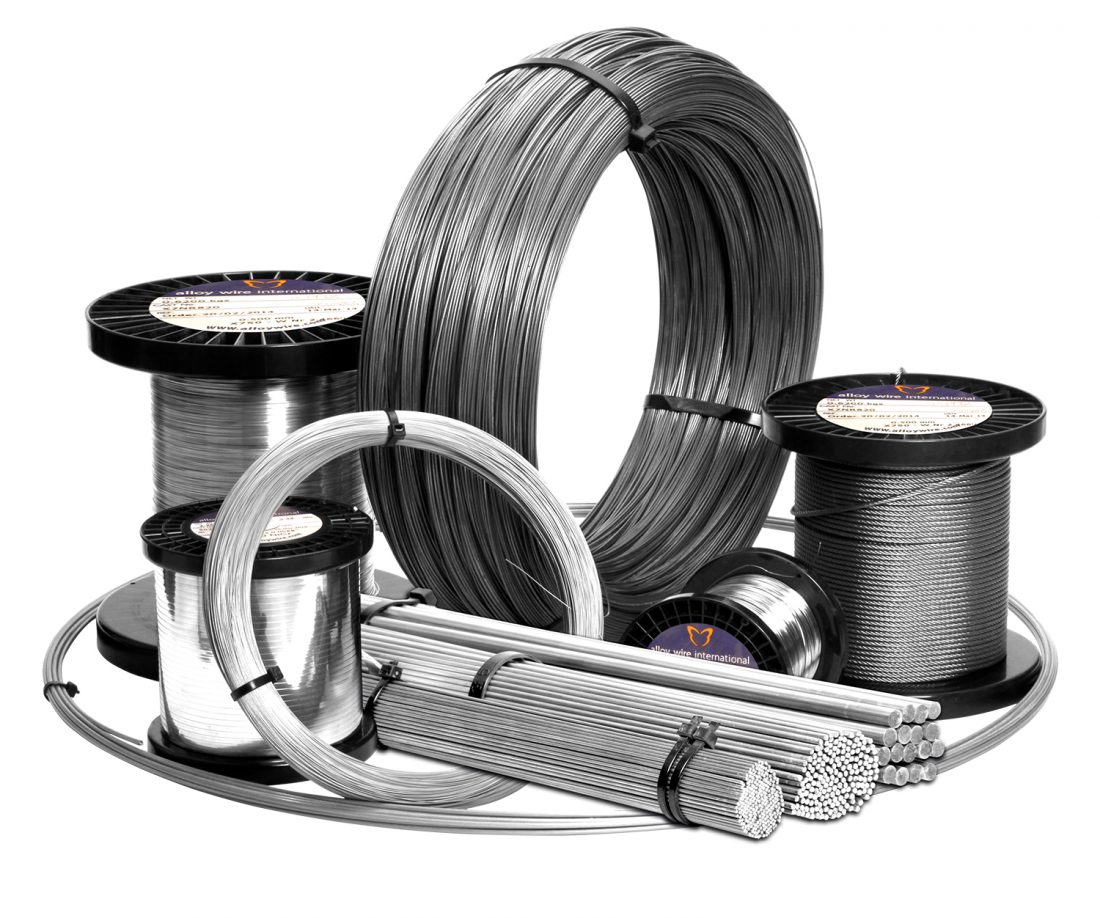
Inconel® 686
This Nickel-Chromium-Molybdenum-Tungsten alloy has exceptional resistance to sulfuric or hydrochloric acids, and to crevice or pitting corrosion in hot acid solutions which out performs Hastelloy C grades in mixed acids.
New Alloy: Inconel® 617 is now available from Alloy Wire. Learn about Inconel® 617
This Nickel-Chromium-Molybdenum-Tungsten alloy has exceptional resistance to sulfuric or hydrochloric acids, and to crevice or pitting corrosion in hot acid solutions which out performs Hastelloy C grades in mixed acids.
Inconel® 617 is a nickel-chromium-cobalt-molybdenum alloy, with a similar high temperature resistance to Inconel® 600/601 with improved strength, while offering comparable corrosion resistance to Inconel® 625. On top of its combination of stability, strength and oxidation resistance at high temperatures, Inconel® 617 also provides resistance in several corrosive aqueous environments.
316 Ti has better high temperature strength and mechanical strength than 316L, thanks to the additions of Titanium, which means Stainless Steel 316Ti can be used for extended periods at elevated temperatures without compromising its corrosion resistance. Stainless Steel 316Ti is also known as AISI 316Ti, Supra316Ti, Nirosta 4571, Polarit 761, and Remanit 4571.
Regarded as ‘Medical Grade’, Stainless Steel 316LVM is vacuum melted to achieve the extremely high levels of purity and ‘cleanliness’ required for surgical implants. It has excellent resistance in physiological environments, to general and intergranular corrosion, to pitting and crevice corrosion. These characteristics make it ideal for both medical application and high precision electronics. Stainless Steel 316LVM is also known as AISI 316LVM.
Stainless Steel 316 has slightly better corrosion resistance than 302 and 304, and also has better non-magnetic properties. Stainless Steel 316 shows excellent corrosion and oxidation resistance in a range of atmospheric environments and corrosive media. Stainless Steel 316 is also known as AISI 316.
Stainless Steel 304 is the most widely used stainless steel, and like 302, it has good mechanical properties and corrosion resistance. This alloy can withstand attack in a range of corrosive media, and its durability makes it easy to sanitise, meaning it is ideal for kitchen and food applications. Stainless Steel 304 is also known as AISI 304.
Stainless Steel 302 has good mechanical properties and corrosion resistance, and is well known for its ease of fabrication and formability. Stainless Steel 302 is also known as AISI 302.
Nitronic 50 exhibits corrosion resistance and that is superior to type 316 Stainless Steel. It has good mechanical properties at ambient and sub-zero temperatures. Unlike other austenitic stainless steels, it does not become magnetic when cold worked or cooled to sub-zero temperatures. Nitronic 50 is therefore considered for applications in the oil & gas, offshore, chemical and marine industries. Nitronic 50 is also known as Aquamet 2, Aquamet 22, and Temet 25.
Duplex stainless steels are magnetic and are far more corrosion resistant than more commonly used stainless grades, i.e. 302 and 316. Super Duplex combines aspects of both austenitic and ferritic grades, and is known for its excellent corrosion resistance and high strength. Super Duplex is also known as Alloy 32750 and SAF 2507.
Duplex stainless steels are magnetic and are far more corrosion resistant than more commonly used stainless grades, i.e. 302 and 316. Duplex is characterised by its high yield strength, as well as good fatigue strength and excellent corrosion resistance. Duplex is also known as Duplex 2205 and Cronifer 2205 LCN.
A commercially pure Nickel (typically 99.6% Nickel), Nickel 201 is essentially the same as Nickel 200, but with a lower carbon content to prevent embrittlement by inter granular carbon at temperatures over 315°C (600°F). Lower carbon content also reduces hardness, which makes it ideally suited for spinning and cold forming. It is also preferred to Nickel 200 for applications involving exposure to temperatures above 315°C (600°F). Nickel® 201 is also known as Phyweld 201.
This Nickel-Copper alloy is precipitation hardenable, due to the additions of Aluminium and Titanium. It combines the corrosion resistance of Monel 400 but gives the added advantage of extra strength and hardness (as a result of its age hardening ability). Monel® K-500 provides corrosion resistance in several marine and chemical applications. Monel® K-500 is also known as Nicorros Al.